Doubs
Plastiform investit dans une technologie d’avenir
Spécialiste du thermoformage, Plastiform prévoit d’investir 4,5 millions d’euros dans un nouvel atelier sur son site de Thise (Doubs). Avec le soutien du plan de relance, l’entreprise mise sur une nouvelle technologie de plastronique.
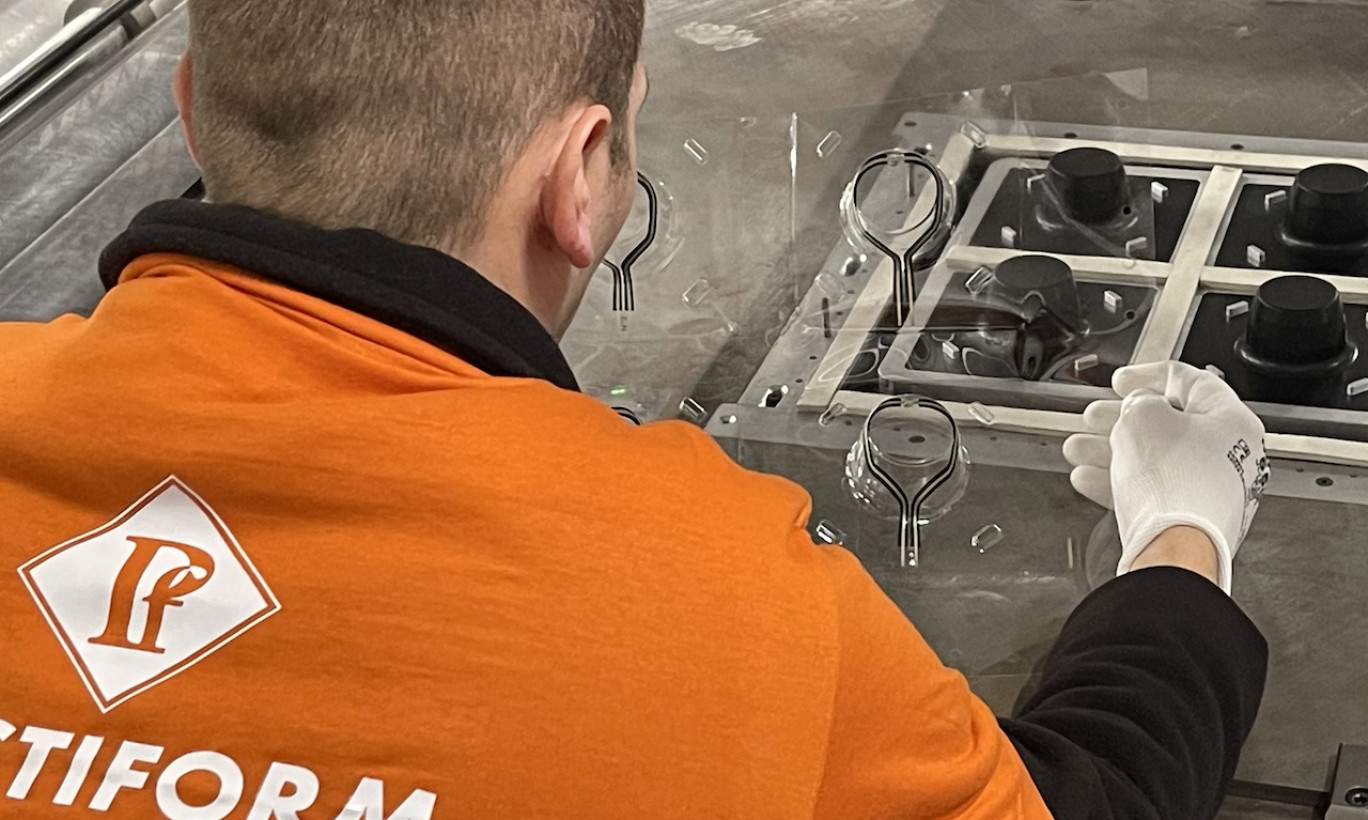
Depuis cinq ans, Plastiform, en collaboration avec Schneider, travaille au développement de la technologie IME, In Mold Electronics. Spécialiste en usinage de précision et en transformation des matières plastiques, l’entreprise intervient dans les domaines de l’aéronautique, du médical, de la micromécanique, de l’énergie, de l’habitat, mais aussi de l’automobile. C’est d’abord pour ce dernier secteur que Plastiform s’intéresse à cette nouvelle technologie de plastronique. Celle-ci consiste à associer la plasturgie et l’électronique, dès le processus de création de la pièce, afin de la rendre intelligente sans avoir besoin d’un circuit électronique externe.
Après avoir fait la preuve de concept de la technologie IME, Olivier Rodary, président de Plastiform, se réjouit de franchir une nouvelle étape. « Nous allons créer un atelier de 1 000 m², en salle propre de type ISO 7, autour de l’IME pour l’amener au niveau industriel. » L’investissement, de 4,5 millions d’euros au total, bénéficie du soutien du plan de relance à hauteur de près de 1,5 million d’euros et devrait s’accompagner de cinq recrutements.
Une technique toute en légèreté
Avec ses nouveaux équipements, Plastiform souhaite répondre aux besoins des constructeurs automobiles et à leur problématique de poids. « Appliquée sur une pièce, l’IME permet d’obtenir un gain de place jusqu’à 80 % et un gain de poids jusqu’à 90 %. Cette technologie fait aussi gagner en fiabilité en réduisant le nombre de pièces et en simplifiant les process. » La technologie pourrait ainsi réduire de 30 à 50 kilogrammes le poids final d’un véhicule.
Les nouvelles machines, conçues spécifiquement pour l’entreprise et pour l’IME, pourront traiter deux formats de pièces : Les petits produits, de moins de 50 centimètres, présents dans les habitacles par exemple et les grands, allant jusqu’à 170 centimètres, pour les bandeaux à l’arrière d’un véhicule notamment. « Nous pourrons aussi concevoir des faces avant de machine à laver ou des équipements pour le milieu médical », précise Olivier Rodary, envisageant d’autres débouchés pour son atelier qui devrait être opérationnel en 2023.
Une technologie d’avenir
Pour l’entreprise aux 25 salariés, la technologie IME ouvre de nouveaux horizons. « Il n’y a qu’une dizaine d’acteurs dans le monde à travailler sur ce secteur pour le moment. » Le dirigeant évoque en parallèle une étude de marché annonçant un développement croissant de l’IME d’ici à 2023 – 2025.
« Nous pouvons intervenir comme bureau d’étude en amont d’un projet ou aller jusqu’à la conception. » Avec un chiffre d’affaires de 3,2 millions d’euros en 2020, Plastiform s’est spécialisé à la fois dans les pièces techniques thermoformées et dans le conditionnement pour les industriels.
Pour Aletheia Press, Nadège Hubert